高溫排膠爐是陶瓷、電子、新材料等領(lǐng)域的核心設(shè)備,其核心功能是通過可控高溫環(huán)境實(shí)現(xiàn)材料中有機(jī)粘結(jié)劑、塑化劑及水分的去除。這一過程涉及熱解反應(yīng)、氣體擴(kuò)散、精密控溫三大技術(shù)模塊的協(xié)同運(yùn)作,直接影響最終產(chǎn)品的致密性、純度及性能穩(wěn)定性。
1.熱解反應(yīng):分子級分解的精準(zhǔn)控制
當(dāng)爐內(nèi)溫度升至200-500℃時,材料中的有機(jī)粘結(jié)劑(如聚乙烯醇、石蠟)開始發(fā)生熱分解。以陶瓷基板制造為例,聚乙烯醇在300℃左右分解為二氧化碳、水蒸氣及碳?xì)浠衔?,而石蠟則在250-400℃范圍內(nèi)逐步氣化。排膠爐通過分段升溫程序(如5℃/min的勻速升溫+特定溫度平臺保溫),確保不同粘結(jié)劑在各自最佳分解溫度區(qū)間內(nèi)完成反應(yīng),避免因溫度過高導(dǎo)致材料開裂或過低殘留雜質(zhì)。例如,某型號排膠爐采用50段可編程PID控溫系統(tǒng),可精確模擬粘結(jié)劑的熱重分析曲線,將分解殘留率控制在0.1%以下。
2.氣體擴(kuò)散:動態(tài)平衡的工程優(yōu)化
分解產(chǎn)生的小分子氣體需通過擴(kuò)散作用從材料內(nèi)部遷移至表面。排膠爐通過雙層殼體結(jié)構(gòu)與風(fēng)冷循環(huán)系統(tǒng),在爐膛內(nèi)形成均勻的熱對流場,加速氣體擴(kuò)散速率。以1100℃排膠爐為例,其爐膛內(nèi)表面涂覆進(jìn)口氧化鋁涂層,反射率高達(dá)92%,配合310S合金排膠盒的負(fù)壓設(shè)計,使氣體在盒內(nèi)形成螺旋流場,顯著提升擴(kuò)散效率。某企業(yè)實(shí)測數(shù)據(jù)顯示,采用該設(shè)計的排膠爐可將排膠周期從12小時縮短至8小時,同時將材料內(nèi)部孔隙率降低至0.5%以下。
3.精密控溫:納米級均勻性的技術(shù)突破
溫度均勻性是排膠工藝的核心指標(biāo)。現(xiàn)代排膠爐采用硅碳棒或硅鉬棒作為發(fā)熱元件,結(jié)合微晶體纖維爐膛與智能溫控系統(tǒng),實(shí)現(xiàn)±1℃的控溫精度。例如,某型號1600℃排膠爐通過多區(qū)獨(dú)立控溫技術(shù),將600×500×500mm爐膛內(nèi)的溫差控制在3℃以內(nèi),確保大尺寸陶瓷坯體排膠一致性。此外,部分高級設(shè)備配備激光氣體分析儀,實(shí)時監(jiān)測排氣成分并反饋調(diào)節(jié)升溫速率,形成閉環(huán)控制系統(tǒng)。
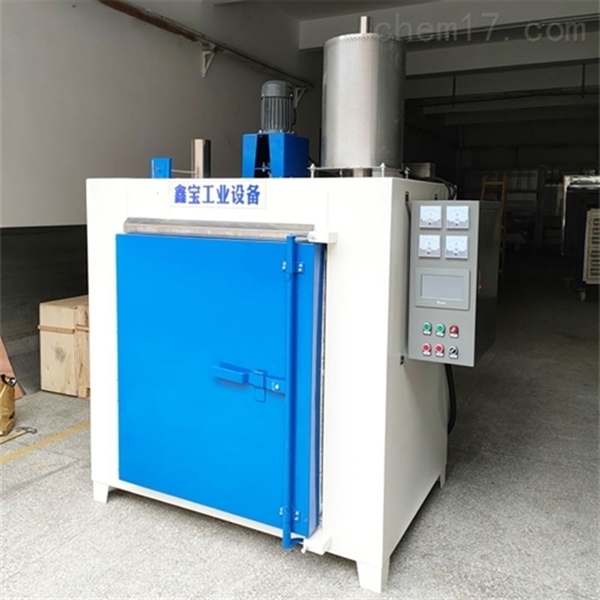
從分子熱解到氣體擴(kuò)散,再到精密控溫,高溫排膠爐通過多物理場協(xié)同作用,為新材料制造提供了關(guān)鍵工藝保障。隨著第三代半導(dǎo)體、3D打印陶瓷等新興領(lǐng)域的發(fā)展,排膠爐正朝著更高溫度(1800℃)、更精準(zhǔn)控溫(±0.5℃)、更智能化的方向演進(jìn),持續(xù)推動材料科學(xué)的技術(shù)邊界。